Innovation of Automation – DWM Magazine – DWM Magazine
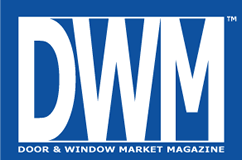
Innovation of Automation
Every window and door manufacturer is doing all they can to automate their build and assembly process. We all understand the labor challenges will continue, and we want to make the most of the great people we have now. The real application of innovation is needed to make automation succeed, and the real challenge is what you must do BEFORE you automate!
I advise a three-step approach to evaluate your “Automation Readiness.” Those steps are:
1. Product readiness. The automating of a difficult and defect-prone design can put good money after bad. The design may have been in use for many years and delivered great profits, but our understanding that clever and innovative assemblers have made this design workable must improve! I recall a window design that used five different framing materials before the sash was installed. It had a fiberglass sill, vinyl subframe, metal cladding, polymer jamb liners, and a wood interior. I’m sure your design is not that complex, but you get the point that automating this complexity is not the most effective way. It’s best to complete a Design For Assembly (DFA) analysis to start and improve your design and lower your part count prior to automating. The benchmark for a good part count is sub 100 on a vertical sliding design. Check yours against this benchmark.
2. Process readiness. Automation studies need to be proceeded by a thorough Value Stream Map (VSM) to determine how the new machinery will fit into the process. If your production line is set for a takt time of 30 seconds (two doors are completed for every production minute, does your automation match it? Is it scalable? We also see too often a new automation center does not live up to its advertised output. It is best to test and pilot run production on the new machines before insertion into the line. Remember that automation that produces too many parts can be as disruptive as too few. If your downstream line cannot handle the output, your Work In Process (WIP) will balloon. Another key part of process readiness is zero defect readiness. This process identifies common product defects and passes that information to the automation builder. The builder then creates either devices or camera-based inspection processes into the machines that do not allow common defects to be passed on. The machine either stops or segregates the defective part. Eliminating waste in your process and refining your takt, station balance, and bottlenecks will allow your automation investment to pay off.
3. People readiness. How we prepare and train our people for operation and maintenance of automation is one of the most important steps. Safety always comes first, so ensuring the proper guarding and sensors are in place is primary. We should always require fail-safe control by redundant devices. For example, if a sensor fails-a light curtain should prevent machine operation if the operator is in the danger zone. Secondly, the operators must be trained in the effective operation of the machine and its Total Productive Maintenance (TPM) requirements. During the pilot operation, make sure that the key operators are running the machines. Third, place great emphasis on downtime elimination by training your maintenance techs in the proper Preventative Maintenance (PM) steps. Some of the new line automation assemblies require more than 30 hours per week in strict PM to stay running long term. You must plan for additional techs to cover these needs. We also need to continually invest in updating our tech certifications for electronics, pneumatics, and hydraulics. Your automation investment only works with zero downtime, and you can control this!
These steps take lots of thought and work, but they will ensure your investments work!
Keep Innovating!